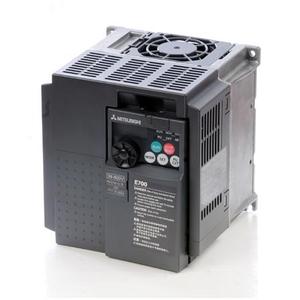
1. Design a special frequency converter room:
When the inverter used has a large power or a large number, a special inverter room can be designed. The door and window of the room and the wall of the cable must be sealed to prevent dust from intruding. Air filter devices and circulation channels must be designed to maintain the normal circulation of indoor air. The room temperature must be kept below 40°C. Unified management is conducive to inspection and maintenance.
2. Install the inverter in the cabinet with the fan and filter device:
When the user does not have conditions to set up a special inverter room, consider creating a dust-proof cabinet for the inverter. Fans and filters designed to ensure adequate air flow inside the cabinet. The user should regularly check the fan to remove the dust on the filter screen to prevent the temperature from exceeding the specified value due to insufficient ventilation.
3, choose a strong dust-proof capacity Inverter:
There are many specifications and models of inverters on the market. When selecting, in addition to price and performance, the adaptability of the inverter to the environment should also be considered. Some frequency converters do not have a cooling fan and rely on their shells to naturally dissipate heat in the air. Compared with an air-cooled type inverter, despite the large size, the device has a good sealing performance, is not affected by dust, is easy to maintain, and has a low failure rate. Long service life, especially suitable for use in corrosive industrial gases and dusts.
4, reduce the inverter no-load running time:
In the industrial production process, general-purpose inverters usually connect the power supply frequently, and control the start/stop of the motor through the “forward/reverse/common†control terminals of the inverter (or the keys on the control panel). turn around. Some devices may be on and off, and the fan is still running when the inverter is unloaded. It will absorb dust, which is unnecessary. During production operations, the inverter's dead time should be minimized to reduce the impact of dust on the inverter.
5, establish a regular dust removal system:
The user should determine the time interval for regular dust removal based on the effect of dust on the inverter. Dust can be purged with an electric vacuum cleaner or compressed air. After dust removal, also pay attention to check the rotation of the inverter fan, check whether the electrical connection is loose heat.
Braces Screw Riveting Drilling
Braces Screw Riveting Drilling,Automatic Screw Fastening Machine Robot,Automatic Screw Fastening Robots,Retainer Tightening Machine
Suzhou Huaweile Automation Technology Co., Ltd , https://www.hwlelocking.com