The process of a dyno test on a Liebherr engine
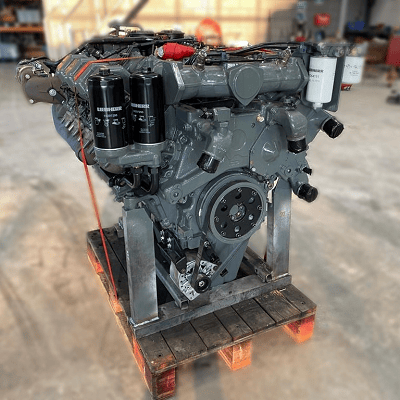
When it comes to heavy machinery, reliability and power are paramount. Liebherr, a name synonymous with innovation and excellence in engineering, stands tall as a pioneer in the realm of heavy equipment and machinery. From towering cranes to robust excavators, Liebherr’s engineering prowess extends to the heart of these machines. We delve into the world of dyno testing a Liebherr engine, uncovering the meticulous process behind unleashing the raw power concealed within.
The foundation of excellence
Before we embark on the journey of dyno testing, it’s crucial to understand the foundation upon which Liebherr engines are built. With decades of engineering expertise and commitment to quality, Liebherr engines are crafted to withstand the most demanding environment and deliver unparalleled performance. Each component is meticulously designed and rigorously tested to ensure reliability, efficiency and longevity.
The process
1 Preparation: The engine undergoes meticulous preparation before being mounted onto the dynamo meter. This includes ensuring all connections are secure, fluids are filled to the appropriate levels, and sensors are properly calibrated.
2 Mounting: The engine is carefully mounted onto the dynamometer, a specialized device designed to simulate real-world operating conditions. Precision is paramount during this step to ensure accurate results.
3 Initial checks: Once mounted, a series of initial checks are conducted to verify proper alignment, connection integrity, and functionality of all engine systems.
4 Warm-up: The engine is started and allowed to warm up to operating temperature. This ensures consistent results and minimizes the risk of damage during testing.
5 Baseline testing: With the engine warmed up , baseline tests are conducted to establish initial performance metrics. This includes measuring power output, torque, fuel consumption, and emissions at various RPM levels.
6 Load testing: The engine is subjected to progressively increasing loads to simulate different operating conditions, such as idle, partial load and full load. This allows engineers to assess performance across the entire operating range and identify any potential issues or optimization.
7 Data analysis: Throughout the testing process, data is continuously collected and analyzed in real-time. Advanced instrumentation and software are used to monitor performance metrics and identify trends or anomalies.
8 Optimazation: Based on the data analysis, adjustments may be made to optimize engine performance. This could involve fine-tuning fuel injection timing, adjusting air-fuel ratios, or optimize turbocharger boost pressure.
9 Validation: Once testing is complete, the results are meticulously reviewed and validated against predetermined criteria and specifications. Any deviations or anomalies are thoroughly investigated to ensure accuracy and reliability.
10 Reporting: Finally, a comprehensive report is generated detailing the results of the dyno testing, including performance metrics, observations, and any recommendations for further optimization or refinement.
The outcome of dyno testing
Dyno testing a Liebherr engine is more than just a routine procedure – it’s a testament to the unwavering commitment to excellence that defines Liebherr’s engineering philosophy. By subjecting their engines to rigorous testing and analysis, Liebherr ensures that each engine delivers the uncompromising performance, reliability, and efficiency that customers expect.
In conclusion, dyno testing a Liebherr engine is not just about measuring power output. It’s about unlocking the true potential of these remarkable engines and ensuring they exceed expectations in the most challenging environments imaginable.
Full Automatic Mattress Machine
Quality products with stable performance
Advanced system with operation easily and conveniently
Space between coils adjusted accurately and flexibly by Servo Motor
High grade protection with hommization design
Artistic design enriching wokshop environment
Automatic mattress machine, roll-packed mattress Packing Machine
1.Mattress wrapping machine is specialized in rolling packing the foam mattress or latex mattress which density is equal or less than 30kgs/m³.It has the following advantages: High production affiance .it takes 35-40seconds to finish one foam mattress rolling packing into the plastic bag. Simple operation: it will be automatic rolling packing if you put on the foam and plastic bag and then push one button. The worker operates the machine skillful after few minutes training. Low packing cost: It needs one PVC or PE bag of diameter 320mm(approx) to pack one foam mattress. The volume of foam mattress can be reduced greatly after rolling packing .Thereby the cost of transportation and storage can be much lower. The machine is compact and convenient to installation and maintenance.
2.The import automatic adjustment, more adaptable, thus improving the thin mattress of the thin mattress, the volume of the thick mattress cannot roll the thin mattress, thoroughly solve the mattress in the process of slipping in the process of serious problems, the minimum adjustment range to 40mm
3.The mattress not only does not deform, but also saves the storage and transportation space for the producers, thus saving the related costs, such as transportation cost and transportation cost. So as to improve the competitiveness of its own.
Mattress Machine,Mattress Machine Price,Mattress Making Machine,Mattress Covering Machine
SOFTLIFE MATTRESS MACHINERY CO.,LTD , https://www.machinesoftlifefoam.com