Guided reading: different coke powder, coke, fine coke powder, coke and coke and other materials, its molding, drying and different types of coke for pressure on the ball, drying equipment design is also very different . Let's introduce it to everyone.
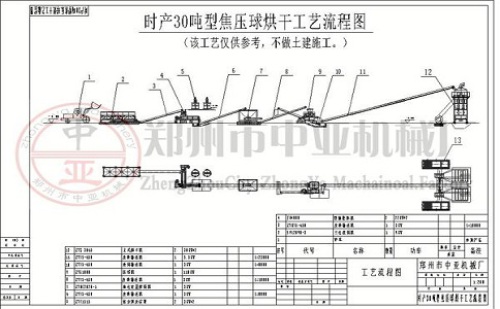
Coke pressure ball, drying process is as follows:
1. Forming of coke forming The first stage: equipped with a quantitative feeding system. This means that the entire production line is “collapsed†due to the uneven production of the production line during the production process. As a result, the entire production line equipment is not matched. As a result, the equipment is not directly proportional to the incoming and outgoing products. What often goes wrong is the normal production and benefits of the customer. Therefore, equipment matching is a key issue.
2. Crushing stage in the second stage of forming of coke: The particle size of the coke forming material is generally 0-3mm, so that the material plays a decisive factor in forming. If the material is more than 5mm, the forming difficulty will increase, and the molding rate will be affected. The forming difficulty will be also less than 1mm and the molding rate will also be affected. Therefore, the general pressure ball size 0-3mm. In contrast, the hardness of coke is not so great, and it is very difficult to crush it. So you can use ordinary grinders.
3, the formation of coke forming the third phase of the material added to the binder, are mixed with: the mixer is divided into the following categories: vertical mixer, horizontal mixer and wheel roller mixer. The selection of the mixer can be determined according to the material conditions of the mixer (for example, the dry humidity of the water, the degree of cleanness of the material, etc.). The following is a brief description of adhesives. There are many types of adhesives. Divided into two major sections: organic and inorganic. Organic and inorganic are wet adhesives and dry adhesives (dry powder series). As the name implies, inorganic binders are nitrogen, lin, and potassium single element binders; organic binders are composite binders, and adhesives produced by chemical units are finished adhesives. There are cold strength, thermal strength, can be more according to the difficulty of molding materials or materials do not allow the addition of other elements and other related issues can be solved one by one.
4, through the above equipment program, the next step is the material pressure ball forming stage, my unit processing pressure ball forming equipment more than 20 years of pressure ball forming equipment is also divided into a variety of. They are mechanical type, constant pressure oblique iron type, butterfly spring type, hydraulic pressure type, high pressure type, spiral pressure high pressure type and so on.
Forming physical moisture is 8% -12%, water exceeding this value will cause the material to stick to the mold affect the molding rate and increase the difficulty of manual processing; moisture below this value will lead to the material molding density can not be achieved, adhesion The agent does not achieve adhesion, low molding rate and other related problems.
5. After the material is formed, the formed pellets are then dried. There are many drying methods for my unit, vertical dryer (round, square), mesh belt dryer, chain plate dryer, box dryer and so on. Select drying equipment according to the size of the molding pellets. Different drying equipment, drying methods are also different.
6, then other coke-related equipment will not give you one by one to explain, the specific configuration or based on their needs, mode of operation and site area, water and electricity and other related issues to choose matching oh. In addition, the connection of each device is connected with the conveyors one by one. Only in this way can an intelligent and automated management system be used. Reprovisioning distribution cabinet automatic integration operation.
Collets and Collet Bodies
Collets directly hold the tungsten in place when you tighten the back cap and create the electrical contact necessary for good current transfer. They are generally made of standard grade copper or tellurium copper.
Collet bodies screw into the TIG torch and accommodate various size tungsten and their respective collets, each of which range in size from .020 to 1/4 inches. They are also made of standard grade copper or tellurium copper.
When choosing collets and collet bodies, you need to consider two main factors.
First is price. Standard grade copper collets and collet bodies are less expensive, but they also tend to be less durable. Less expensive collet and collet bodies are also prone to failure under high temperature applications. After extended use, they do not secure the tungsten as reliably.
Conversely, the more expensive tellurium copper collets and collet bodies have better heat resistance on higher amperage applications. These consumables generally resist twisting or elongating and hold the tungsten more securely after extended periods of use. They also have more tensile strength and less ductility.
You also need to decide between a single- or two-piece system (See figure 1). Typically, manufacturers sell collets and collet bodies separately to match a specific tungsten size. For example, you would purchase a 1/16-inch collet and collet body to match a 1/16-inch tungsten. This system works well and accommodates a wide range of tungsten sizes, especially smaller ones.
Fig. 1 Choosing between a standard two-piece system (top) or a single-piece system (bottom) is one of the factors in determining which collets and collet bodies are best for you.
There are also single piece systems that combine the collet and collet body together. From a performance standpoint, they provide better securing force and are easier to remove when used in a demanding application. The reason for this factor is because the collet mechanism is further away from the heat and less susceptible to heat distortion. They also reduce the possibility of mismatching collet and collet body sizes, allow for quicker tungsten changeover and help simplify parts management.
Collet And Collet Body,Copper Collet Body,Tig Collet Body,Collet Body For Welding Torch
Changzhou Edaweld Trading Company Limited , https://www.edaweld.com