Abstract] Greek third-party logistics provider Diakinis has used UHF technology to track cargo pallets at its distribution centers.
(RFID Radio Frequency Express solemnly declares: If you need to reprint, please obtain the written consent of RFID RF Express and indicate the source to ensure the integrity of the text of our station! - "Regulations on the Protection of Information Network Transmission Rights")
[RFID Newsletter February 15, 2008] Greek third-party logistics provider Diakinis has tracked 1,300 pallets at its distribution center in Athens using EPC Gen 2 RFID tags and RFID readers. Diakinisis began experimenting with RFID applications in 2006 and completed the installation of the system in November 2007, but currently only provides RFID technology applications to an international beverage and food company (unnamed).
It is understood that Alien Technologies is the company that provides RFID hardware for Diakinisis. Diakinis chose Alien's EPC Gen 2 Squiggle and M-type UHF RFID tags and the ALR-8800 RFID reader. At the same time, Greek RFID system integrator Business Effectiveness provided consulting and installation services for the project.
Diakinisis believes that RFID technology is an effective way to provide better service to customers. With the RFID system, manual scanning of barcodes is no longer required to confirm the pallets, saving labor and time; and providing customers with more and more accurate product transport transparency.
Alien's Squiggle tag
Thanks to the RFID system, Diakinis has greatly improved the efficiency of cargo tracking management and warehouse management, and reduced manual errors and related costs. Especially for foods that are sensitive to the product's validity period, distribution errors will bring a lot of losses. At the same time, this is a good customer service because the customer receives what they need and can trace the distribution of these products.
When the goods are shipped to the Diakinis Distribution Center (RFID area: 1.2 million square feet), the original bar code label on the package is scanned and associated with the RFID tag on the tray. When a smart forklift truck is equipped with an onboard computer and an RFID reader, the RFID reader of the forklift reads the pallet label ID and tells the forklift driver through the onboard computer. Compared with the original bar code management system, the forklift driver does not need to get off the bus to scan the bar code. The on-board computer is connected to the company's warehouse management system (WMS), and the driver can transport the pallet to the correct location according to the computer instructions. Alien's M-label is attached to the concrete floor of each storage area of ​​the Diakinisis distribution center, and the Squiggle label is attached to the storage shelf. The forklift reader captures the floor or shelf label data, the computer verifies the location and tells the WMS tray that it has been delivered to this location. If the employee places the pallet in the wrong position, the on-board computer screen will display an error message until the forklift driver correctly parks the cargo. In addition, the onboard computer of the forklift can also receive commands to find the pallet at the specified location and verify it through the reader, so that the correct pallet can be selected. This reduces a lot of errors about product placement, so you can locate the product very quickly.
Alien's M label
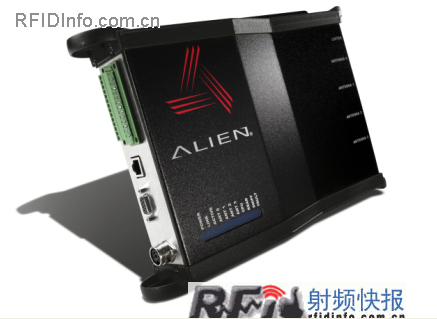
ALR-8800 RFID Reader
Diakinisis also applied Alien EPC Gen 2 RFID tags on transport trucks, which loaded pallets at loading parking and sent them to other distribution centers or stores. At each of the loading parking spaces, the RFID terminal reads the label of each tray loaded with the vehicle and records the RFID tag data. This information is automatically compared to the data in the warehouse management system. If there is an abnormality, there will be a warning of lights and sounds.
Currently, with the help of Business Effectiveness, Diakinisis further applies RFID technology to integrate business processes, such as canceling the waiting step – it is the transport vehicle that has to place the pallet after arriving at the destination and wait for another forklift to transport the pallet to the shelf. Now, Staff can deliver the pallet directly to the shelf upon arrival, avoiding wasted time and repetitive operations.
Automatic packaging machine is generally divided into semi-automatic packaging machine and automatic packaging machine. Automatic packaging machine is mainly used for automatic packaging of food, medicine, chemical industry and plant seeds. The material can be granule, tablet, liquid, powder, paste, etc. The automatic packaging machine has the functions of automatic measurement, filling, bag making, sealing, cutting, conveying, printing production batch number, increasing easy incision, warning without material, mixing, etc.
It is mainly suitable for packing instant noodles, ice cream, biscuits, Weihua biscuits, egg yolk pie, egg roll, bread, sausage, seaweed, frozen food, medicine, medicine board, infusion bag (bottle), soap, soap, mosquito repellent incense, paper towel, toilet paper, card, adhesive tape, disposable tableware (knife and fork), etc.
The automatic packaging machine is advanced in design, reasonable in structure and reliable in performance. The automatic packaging machine adopts double synchronous belt pulling film, which is controlled by the cylinder for tension, automatic deviation correction, automatic alarm protection function, and the maximum loss reduction. The measuring device is matched, and it integrates bag making, filling, filling, printing and counting. The metering device can be modified according to the material opening and closing mode.
Basic characteristics
1. Invention patent: a roll of film is automatically cut and translated into two packaging films on the machine, and two lines of articles are automatically packed. One machine has two capacity, small area, and saves people and energy.
2. Touch screen control, simple operation, intuitive display, modular design of electrical appliances, digital control.
3. There are three driving modes: double frequency conversion, double servo and three axis servo. No mechanical transmission, stable and reliable operation, low noise and high tracking accuracy.
4. Material position adjustment: automatic or jog button adjustment.
5. Material conveying width adjustment: one handle can adjust two rows of conveying width at the same time.
7. Two sets of adjustable bags can adjust the height and width of the bag.
8. There is a traction guide wheel in front of the longitudinal heat sealing wheel, and the traction guide angle can be adjusted during operation
Automatic Multi-Head Packing Machine,Automatic Nut Filling Machine,Automatic Powder Package Machine,Automatic Weighting Package Machine
Glove Industry Co.,Ltd. , https://www.glovemech.com