Electromechanical relays are recognized as reliable, robust low-cost devices. The amount of manufacturing of relays is increasing day by day, and it has been successfully used in myriad applications for signal and energy distribution. Even in the harshest environmental conditions, it still has good robustness and reliability. Various relay types cover a wide range of switching loads, from μV and μA to hundreds of A and up to 500V. Moreover, the relay has a very low resistance (mΩ) in the energized state and a very high insulation resistance (GΩ) in the de-energized state, both of which are suitable for load circuits and control circuits as well as open-circuit switching paths.
The relay has a large overload capacity in terms of allowable voltage, current or temperature. Although the relay has very good physical characteristics, there are some additional requirements. The PCB footprint must be as small as possible and the relay should be splash-proof (wash-proof or weather-proof), or even completely sealed. The new design can not only meet all these requirements, but also improve reliability. Future innovations in relay technology will further enable smaller designs without changing the switching characteristics.
Material cost relays require the use of many raw materials, such as copper for the manufacture of coils or current-carrying parts, noble metals for the production of switching contacts (eg gold, silver and palladium), iron for magnetic circuits, And the plastic used to create the insulation system. The cost of these raw materials has risen significantly in recent years, and the cost of some materials has increased several times. The increase in the cost of silver is particularly serious because there is currently no practical material that can replace silver in switchgear.
One of the main reasons for the great success of miniaturized electromechanical relays is that the relay industry can meet the needs of the electronics industry, telecommunications and automotive electronics equipment through new, miniaturized design innovations (Figure 1). The situation of general-purpose and power relays is more troublesome. The standardized pin layout and necessary air and leakage current paths make the miniaturization design of these relays more difficult, and even hinder the development of miniaturization to some extent. The main challenge in the miniaturization design of relays is to increase the switching capability while reducing the physical size.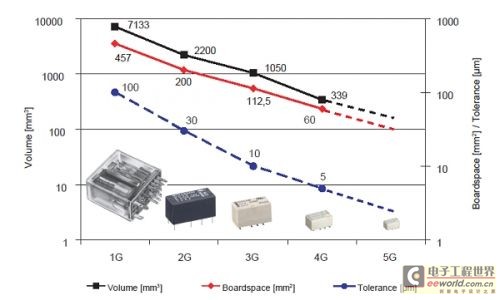
In relay miniaturization design, many constantly changing factors must be considered: maintaining contact reliability in the event of reduced contact force and breaking force; protection of relays from internal and external contamination; material change and contact corrosion The resulting closing force is reduced; in spite of the reduction in physical size, the insulation performance still improves; thermal performance, self-heating and performance at elevated ambient temperatures; longer service life and higher switching capacity; higher Reliability requirements; limitations imposed by manufacturing technology.
New technologies and new concepts will also lead to great innovation in relay technology in the future.
Table 1 shows that the size of the signal relay is continuously shrinking. Although the size is significantly reduced, coil power consumption and switching capacity are almost the same, dielectric characteristics have been improved, switching time has also been significantly shortened, but the thermal resistance has increased.
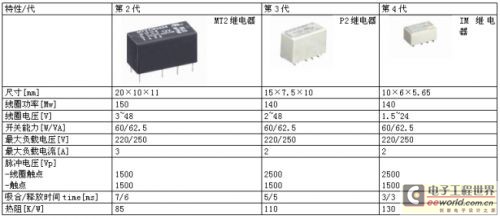
The following are some of the factors that can be used to improve the characteristics while reducing the size of the relay.
Design: All miniature relays use polarized magnetic circuits. This feature allows the physical size to be reduced while also supporting bistable switching characteristics. Coil coating allows significantly reduced relay gap and leakage current paths. The use of an airtight enclosure is another advantage, which is to optimally protect the interior of the relay from external contamination, thereby reducing the minimum contact force required.
Materials: In the miniaturization design process, the ratio of volume to surface area will deteriorate, which will lead to increased thermal resistance. In this case, if you still want to maintain good contact reliability, you need to improve the characteristics of the insulation material used. In order to be able to provide the same or even higher reliability, it is necessary to significantly improve the thermal stability and the exhaust characteristics of the insulating material.
The use of copper material is also very important. The higher the conductivity, the more it is allowed to reduce the necessary cross-section and the smaller the physical shape. For the spring material used, the relaxation at high temperatures is very important.
Process: The miniaturization design puts forward higher requirements on the accuracy of the components used in the relay and the precision of the assembly process. Only when both are controlled can the smaller physical size be effectively achieved. Smaller tolerances in the manufacturing process also result in less dispersion of switching characteristics. The smaller physical dimensions require fully automated production to systematically eliminate human factors during assembly and testing.
The larger dielectric strength design can increase the dielectric strength. This sounds reasonable, but it is not necessarily correct in every situation. As shown in Figure 2, compared to the 3rd generation relay, the dielectric strength of the 4th generation product has significantly increased. This improvement in coil-to-contact and in the open switch path can be achieved first by coating the coils, separating the drive from the switching chamber, using an airtight enclosure and a suitable inert gas.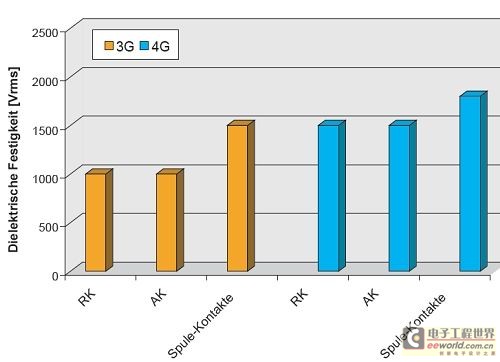
With these measures, although the physical size is reduced by 2/3, the dielectric properties can still be enhanced by 50%.
Switching Capability Many people believe that larger designs can handle larger switching loads and, therefore, longer service life. As the example shown in Figure 3, the fact is not necessarily the case. As can be seen from Figure 3, the 4th-generation relay, which is much smaller than the 3rd-generation relay, can achieve much higher switching performance. The 3rd-generation relays can only achieve just over 200,000 switching operations, while the 4th generation relays can still operate normally after more than 600,000 switching operations. The miniaturization design can improve the switching characteristics because it has a smaller moving mass, less energetic bouncing, a generally faster switching process, and a shorter arc duration resulting therefrom.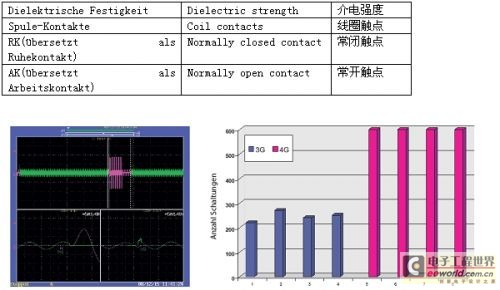
Switching Noise In many applications, especially in automotive or residential environments, acoustic switching noise will be perceived as interference. The miniaturized design has much lighter moving mass and therefore can greatly reduce switching noise. The average noise level generated by the 2nd generation signal relay is 53.5dB (Figure 4), and it can be reduced to 39.6dB for the 3rd generation product, while the noise of the 4th generation relay can be reduced to 28.2dB. Noise levels below 30dB are generally not noticeable even in quiet rooms such as bedrooms.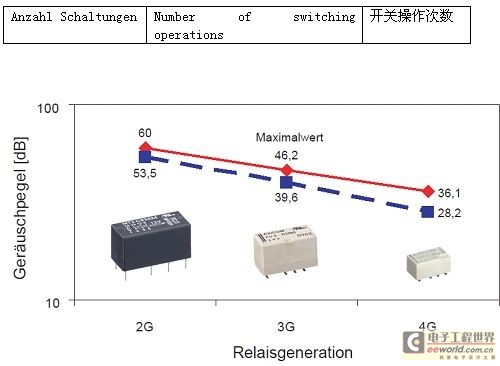
Prospects Electromechanical relays have been successfully marketed for several decades and will continue to be with us faithfully in the future. This relay is highly reliable, robust, and very cost-effective, and it is very easy to use. In modern electronic devices, they are used more and more widely. Contrary to some predictions, it has not been replaced by semiconductor devices so far, but it has coexisted with it peacefully.
The relay has a large overload capacity in terms of allowable voltage, current or temperature. Although the relay has very good physical characteristics, there are some additional requirements. The PCB footprint must be as small as possible and the relay should be splash-proof (wash-proof or weather-proof), or even completely sealed. The new design can not only meet all these requirements, but also improve reliability. Future innovations in relay technology will further enable smaller designs without changing the switching characteristics.
Material cost relays require the use of many raw materials, such as copper for the manufacture of coils or current-carrying parts, noble metals for the production of switching contacts (eg gold, silver and palladium), iron for magnetic circuits, And the plastic used to create the insulation system. The cost of these raw materials has risen significantly in recent years, and the cost of some materials has increased several times. The increase in the cost of silver is particularly serious because there is currently no practical material that can replace silver in switchgear.
One of the main reasons for the great success of miniaturized electromechanical relays is that the relay industry can meet the needs of the electronics industry, telecommunications and automotive electronics equipment through new, miniaturized design innovations (Figure 1). The situation of general-purpose and power relays is more troublesome. The standardized pin layout and necessary air and leakage current paths make the miniaturization design of these relays more difficult, and even hinder the development of miniaturization to some extent. The main challenge in the miniaturization design of relays is to increase the switching capability while reducing the physical size.
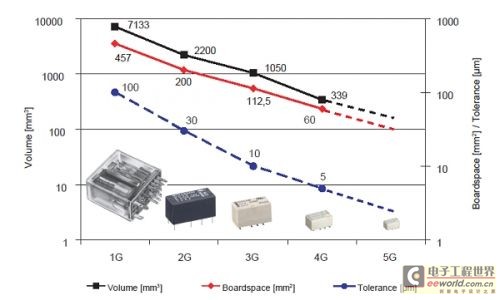
Fig. 1: Miniaturization of signal relays in the past 40 years (Generation 1 to 4).
In relay miniaturization design, many constantly changing factors must be considered: maintaining contact reliability in the event of reduced contact force and breaking force; protection of relays from internal and external contamination; material change and contact corrosion The resulting closing force is reduced; in spite of the reduction in physical size, the insulation performance still improves; thermal performance, self-heating and performance at elevated ambient temperatures; longer service life and higher switching capacity; higher Reliability requirements; limitations imposed by manufacturing technology.
New technologies and new concepts will also lead to great innovation in relay technology in the future.
Table 1 shows that the size of the signal relay is continuously shrinking. Although the size is significantly reduced, coil power consumption and switching capacity are almost the same, dielectric characteristics have been improved, switching time has also been significantly shortened, but the thermal resistance has increased.
Table 1: Key characteristics of 2nd to 4th generation signal relays.
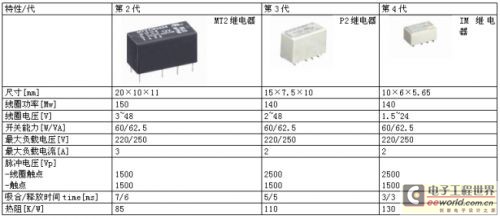
The following are some of the factors that can be used to improve the characteristics while reducing the size of the relay.
Design: All miniature relays use polarized magnetic circuits. This feature allows the physical size to be reduced while also supporting bistable switching characteristics. Coil coating allows significantly reduced relay gap and leakage current paths. The use of an airtight enclosure is another advantage, which is to optimally protect the interior of the relay from external contamination, thereby reducing the minimum contact force required.
Materials: In the miniaturization design process, the ratio of volume to surface area will deteriorate, which will lead to increased thermal resistance. In this case, if you still want to maintain good contact reliability, you need to improve the characteristics of the insulation material used. In order to be able to provide the same or even higher reliability, it is necessary to significantly improve the thermal stability and the exhaust characteristics of the insulating material.
The use of copper material is also very important. The higher the conductivity, the more it is allowed to reduce the necessary cross-section and the smaller the physical shape. For the spring material used, the relaxation at high temperatures is very important.
Process: The miniaturization design puts forward higher requirements on the accuracy of the components used in the relay and the precision of the assembly process. Only when both are controlled can the smaller physical size be effectively achieved. Smaller tolerances in the manufacturing process also result in less dispersion of switching characteristics. The smaller physical dimensions require fully automated production to systematically eliminate human factors during assembly and testing.
The larger dielectric strength design can increase the dielectric strength. This sounds reasonable, but it is not necessarily correct in every situation. As shown in Figure 2, compared to the 3rd generation relay, the dielectric strength of the 4th generation product has significantly increased. This improvement in coil-to-contact and in the open switch path can be achieved first by coating the coils, separating the drive from the switching chamber, using an airtight enclosure and a suitable inert gas.
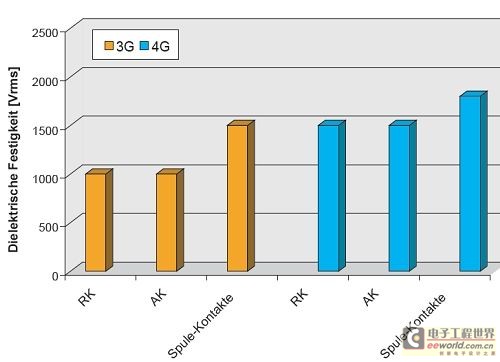
Figure 2: Comparison of dielectric strength of 3rd and 4th generation signal relays.
With these measures, although the physical size is reduced by 2/3, the dielectric properties can still be enhanced by 50%.
Switching Capability Many people believe that larger designs can handle larger switching loads and, therefore, longer service life. As the example shown in Figure 3, the fact is not necessarily the case. As can be seen from Figure 3, the 4th-generation relay, which is much smaller than the 3rd-generation relay, can achieve much higher switching performance. The 3rd-generation relays can only achieve just over 200,000 switching operations, while the 4th generation relays can still operate normally after more than 600,000 switching operations. The miniaturization design can improve the switching characteristics because it has a smaller moving mass, less energetic bouncing, a generally faster switching process, and a shorter arc duration resulting therefrom.
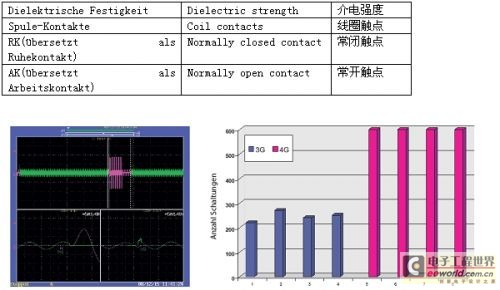
Figure 3: Switching capability of the 3rd and 4th generation signal relays (AC voltage 24V, energizing current 5A, off-current sensing current 1A). The contact voltage is limited to 80V by a varistor.
Switching Noise In many applications, especially in automotive or residential environments, acoustic switching noise will be perceived as interference. The miniaturized design has much lighter moving mass and therefore can greatly reduce switching noise. The average noise level generated by the 2nd generation signal relay is 53.5dB (Figure 4), and it can be reduced to 39.6dB for the 3rd generation product, while the noise of the 4th generation relay can be reduced to 28.2dB. Noise levels below 30dB are generally not noticeable even in quiet rooms such as bedrooms.
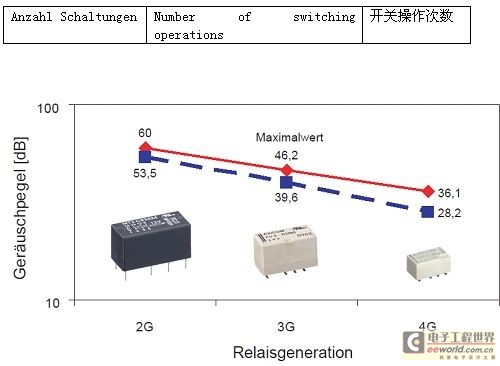
Figure 4: The average and maximum values ​​of the switching noise from the 2nd generation to the 4th generation relays show a decreasing trend.
Prospects Electromechanical relays have been successfully marketed for several decades and will continue to be with us faithfully in the future. This relay is highly reliable, robust, and very cost-effective, and it is very easy to use. In modern electronic devices, they are used more and more widely. Contrary to some predictions, it has not been replaced by semiconductor devices so far, but it has coexisted with it peacefully.
Rod End Bearing,Rod End Jiont Bearing,Stainless Steel Rod End Bearing
Ruihode Bearing Co., Ltd. , http://www.sdrollerbearing.com